PROJECT STORY O1
新たな価値を追求し
開拓するトリガーとなる、
「スマートファクトリーの実現」
への取り組み。
INTRODUCTION
「スマートファクトリー」――これは一般的にデジタルデータの活用によって業務プロセスを改革し、品質・生産性の向上を継続的に実現する工場とされている。それは生産現場のみならず、設計から製造、保守、物流までのビジネスプロセス全体を変革する試みであり、工場の最適化にとどまらず企業全体の取り組みにも拡がっている。日本の製造業はこれまでも各メーカーが積極的に生産性改善に取り組んできた。しかし、人口減少による人手不足や新興経済国の躍進、景気低迷による設備投資の低迷など課題は山積している。競争力のある製造業へ復活・再生させることは国をあげての命題となっているのだ。そうした中、京セラドキュメントソリューションズは、京セラグループの中でも積極的にスマートファクトリー実現への取り組みを開始した。
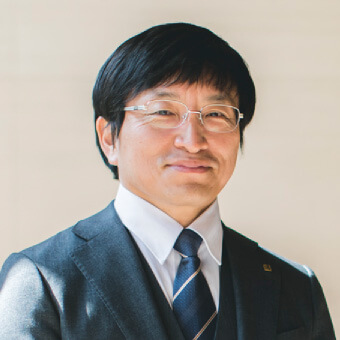
- 小西 英向HIDEHISA KONISHI
-
プリンティングプロダクト事業本部
生産技術統括部 部長
STORY O1
「人ありき」の生産体制からの脱却
京セラグループの「生産性倍増」計画
始まりは2016年にさかのぼる。現在、プリンティングプロダクト事業本部の生産技術統括部長を務める小西英向は、当時、設計部門で複合機開発のプロジェクトリーダーを担当していた。小西らのチームが生み出した複合機は品質が飛躍的に向上した製品として、市場からは高い評価を獲得した。しかし小西には、当時からある問題意識があった。複合機は数千点にも上る部品で構成される精密機械であり、生産はすべて人の手によって組み立てられている。他の製造業においては自動化が進展していたが、複合機の自動化はその構造上の特性から、生産の自動化は難しいとされていた。しかし、果たしてそこに甘んじていていいのだろうか。と小西は考えていた。
「多くの人手が必要ということは、それだけコストを押し上げます。したがって、価格競争力確保のために必然的に海外での生産にシフトすることになります。人の手で組み立てるにあたって、問題になるのはコストだけではありません。品質にバラツキも生まれますし、最終工程で改修が必要なケースもあります。従来のやり方では、最終品質は担保されますが、さまざまなムダも生じてしまうのです。このまま人ありきの生産手法では、将来ものづくりにおける競争に勝ち残れないのではないかという強い危機感がありました。そこで次の世代ではどのようなものづくりが最適なのか、頭の中で構想を練り始めたのです」。
小西のこうした問題意識や危機意識は、やがて困難とされていた複合機の生産自動化へのチャレンジにつながっていく。年が明けた2017年、京セラグループは早期の売上高2兆円達成に向けた取り組みの一環として「生産性倍増」というグループの方針を掲げた。生産性倍増には飛躍的な生産性の向上が求められる。その核心にあったのが、製造ラインの無人化・自動化をはじめとした「スマートファクトリーの実現」だった。それは小西の考えや構想と軌を同じくするものだった。
STORY O2
「自動化対応」への設計手法の変革
デジタル化による生産現場の一元管理
「京セラグループが掲げた方針を受けて、ものづくりの本質的な変革の時代が始まるという直感がありました。そして構想をさらに練り直す中で着想したのは、自動化などによって生産現場を変えるために、設計そのものを変える必要があるということです。自動化とは、それまで人の手によって行われていた組立工程をロボットに置き換えることですが、ロボットは人のように柔軟には動いてはくれません。つまり、設計そのものを自動化あるいはデジタル化を見据えた手法に変える必要がありました。私にとって、この設計変革こそがスマートファクトリー実現への第一歩になったと思っています」。
小西のいう設計変革は、業界でも前例のない「自動化対応設計」の実践であり、それは設計者のスキル向上のみならず意識改革をも必要とするものだった。そして、2017年から始まったこの取り組みにより、生産現場の自動化も並行して進められている。複合機の生産現場は、精密な部品で構成された各モジュール(ユニット)の組み立て、それらを格納する本体フレーム組み立て、そしてマテハン(マテリアルハンドリング=搬送機器)へと展開していくが、現在、各モジュールの自動化にめどが立ち、複合機本体のフレームを組み立てる自動化のトライアルが始まっている。
さらに「スマートファクトリーの実現」において極めて重要な要素となるのが、デジタル化である。ここでいうデジタル化とは、QCD(Quality=品質、Cost=コスト、Delivery=納品)におけるデータを吸い上げ、データの可視化やデータ活用によって生産性向上や品質の安定を図るとともに、小西曰く「QCDを手のひらに乗せる」ことで、経営ドリブンといわれる、データを用いた経営の意思決定を実現することだ。
「MOMと呼ばれる製造オペレーション管理システムを、今年中には導入する計画です。MOMは全ての生産過程をデジタル化して一元管理するもので、データを連携・統合し、生産のパフォーマンスを高めていくためのシステムです。MOMを実装したデジタルプラットフォームの構築で、生産現場(QCD)データのリアルタイムな分析が可能となります。まだ初動段階ですが、これから急ピッチでデジタル化を行い加速していきたいと考えています」。
STORY O3
複合機生産の全自動化、無人化への挑戦
先進的工場「ライトハウス」認定を目指して
「スマートファクトリー」実現への試みは、生産拠点の一つである大阪枚方工場で進められている。組織横断的に約40名からなるプロジェクトチーム「AMS=Advanced Monozukuri Strategy」も発足され、システムと自動化設備のデータ連携を含めた流れの検証が進められている。近い将来には、海外拠点にも展開していく考えだ。また、生産自動化の要素の一つである「マテハン」では、設備を研究するラボを工場内に設置した。これはAGV(無人搬送車)などのマテハン設備の自社開発の取り組みであり、将来的には京セラグループ内への横展開や、さらにその先へも視野に入る。
「単にマテハンを展開するということではありません。資材や部品、仕掛品などの搬送・場内物流の自動化においてプレゼンスを発揮できれば、その先の自動化にもつながり、新しいものづくりをわれわれがけん引する立場に立つことも可能になります」。
マテハン設備の展開を見据えつつ、小西は「スマートファクトリー」の将来ビジョンをどのように描いているのだろうか。
「スマートファクトリーは、その名が示すように“賢い工場”と捉えられがちですが、重要なのは新たな価値を創造することです。スマートファクトリーによる究極の生産性改善には、価格競争力や生産性の向上のみならず、そこから新規事業やイノベーションが生まれる可能性を多分に秘めています。スマートファクトリーは、そうした新たな価値を追求し開拓していくトリガーになると思っています」。
加えて、スマートファクトリーの一つのカタチとして目標に掲げているのが、複合機生産の全自動化、すなわち無人化の実現だ。
「非常に高いハードルですが、ものづくりに関わる全てのメンバーとともにチャレンジしていきたいと考えています。それが実現すれば、これまでのように、コストメリットを考慮して生産する場所(国)を選ぶ必要がなくなり、もちろん日本国内でも生産が可能となります。私個人としては、日本のものづくりの復活・再生にために国内生産にも回帰していく必要があると考えているのです。それによって、日本が培ってきたものづくりの強みが生かせることに繋がっていくと思っています」。
官民連携の国際機関である世界経済フォーラムには、世界で最も先進的な工場を「ライトハウス(Lighthouse、灯台=指針)」として認定する制度がある。世界で約90の工場が認定されているが、日本はわずか2カ所。小西たちは、スマートファクトリーの実現で自社工場が「ライトハウス」の認定を得ることも目指している。それによって国内外の顧客から、京セラドキュメントソリューションズのものづくりが、より高い信頼を獲得することも新たな価値の創造にほかならない。