Home > Sustainability > Society > Approaches to Raising Quality and Customer Satisfaction Levels
Approaches to Raising Quality and Customer Satisfaction Levels
At Kyocera Document Solutions Group, the customer comes first at every step of the product life cycle, from planning, development and manufacturing, to sales, use, support, and recycling.
Quality Policy
The Kyocera Group has established the Kyocera Quality Policy in order to ensure the customer is always satisfied. In order to be a company that is trusted around the world, it is imperative that all our departments adhere to this policy as they do the best job possible. Everyone at the Kyocera Group continues to strive in their capacity to do every job right the first time with the aim of making Kyocera a global leader in quality.
Kyocera Quality Policy
- 1. Kyocera places top priority on our environmental management and product safety systems.
- 2. Kyocera provides products and services to our customers that exceed their expectations by putting them first.
- 3. Kyocera aims to be a world leader in quality by doing every job right the first time.
Product Safety Policy
Safety is the top priority for all products made or sold by Kyocera. Regardless of form or function, they must not endanger a person's life or well-being, nor inflict damage on property. Working upon this foundation, Kyocera has established a product safety policy in addition to its quality policy. Kyocera has also developed Product Safety System Guidelines that provide a concrete code of action at all levels of corporate activity. Additionally, the Guidelines for Product Safety Labeling serve as supplementary guidelines for understanding international standards relating to safety labels.
Kyocera Product Safety Policy
- 1. Kyocera is fully acquainted with the latest information related to product liability and product safety.
- 2. Kyocera maintains an industry-leading standard of product safety.
- 3. Kyocera systematically practices product safety in accordance with manuals.
Quality Management Systems
The Kyocera Group (Japan) regularly holds meetings of the Kyocera CS* Improvement Committee, where the president serves as chair, to improve customer satisfaction indicators and share quality information with the aim of preventing quality problems from occurring or recurring. The group has established quality management systems based on ISO 9001. Each business unit sets its own quality targets and makes quality improvements to achieve those targets. Furthermore, these improvement activities are continuously being upgraded via different types of quality-related training. The training is designed to give employees hands-on training on Kyocera-style tree diagrams and help them enhance their practical skills to effectively respond to quality related problems.
* Customer Satisfaction
ISO 9001 Integrated Certificate pdf
ISO 9001 Certification Statuspdf
Quality Assurance
Our quality assurance department performs premarket assessments and various types of reliability tests as well as verification tests under real-use conditions to ensure that our products will always operate stably during use by the customer. We value the feedback we get from customers via after-sale support and incorporate it into the designing of future products and ensure that the PDCA (plan-do-check-act) cycle of quality management continues running throughout the entire manufacturing process. In order to provide our customers with even better products, we are enhancing our quality assurance system with a focus on the following.
- 1. Improving reliability verification by incorporating new evaluation methods and verification techniques aimed at preventing quality problems
- 2. Changing manufacturing quality control by ensuring quality throughout all manufacturing processes
- 3. Enhancing the quality of service support in the market to ensure products can be used with greater confidence
- 4. Maintaining and managing quality systems on an ongoing basis to better ensure quality
Innovations in Evaluation
The quality assurance department is responsible for evaluating products to determine whether they are marketable, taking corrective measures when any problem is found after sale, and preventing recurrences. While the department at one time evaluated the quality of our products using criteria that were based on past data and experience, this wasn't the best method to meet consumers' changing needs or the needs of customers in countries around the world who may use our products under different conditions. That's why, before evaluating a new product to be marketed, our evaluation staff look at the evaluation criteria in light of the situations where the product will be used and the conditions under which it will be used after gaining an understanding of the new technology behind the product, design changes, operating requirements, and factors that affect the way it works. Then all quality assurance department personnel discuss the evaluation criteria, including potential problems that could arise, and add more parameters by incorporating a perspective that encompass the full scope of their collective insights and foresight. This enables them to conduct product evaluations that address issues that may have been overlooked with the previous criteria. This evaluation method allows us to look more closely into the quality of products to be sold and prevent potential problems at the development stage, making them more reliable and more satisfying to the customer.
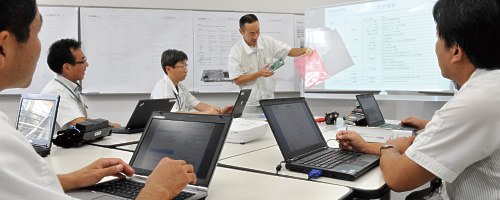
Innovations in Verification
We are working on innovations in verification techniques. In accordance with our past evaluation standard, we used to make pass/fail decisions based on whether or not a product satisfied the functions and performance described in the product specifications. Today, we conduct verification testing that looks at not only performance deviations during mass production and measures to prevent the causes of such deviations, but also the behavior of parts and components under the conditions where the product will be marketed. We are also focusing on identifying the limits of a product with an understanding of the technology behind it and conducting verification tests to detect failure modes when the limits are exceeded.
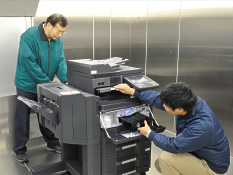
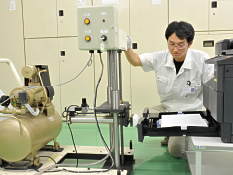
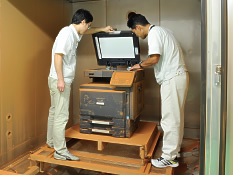
Innovations in Information Gathering
Our market support team plays the important role of gathering information from sales companies all over the world. Serving as a contact point for inquiries and malfunction information from sales companies, the team works with relevant departments to investigate problems and respond to inquiries. It is also responsible for making sure user feedback is incorporated into the development of future models in order to improve product quality. To eliminate delays in information gathering due to time differences and distances between overseas offices, the market support team holds daily meetings with technical supervisors at umbrella sales companies. Exchanging information directly with sales companies every day enables the team to respond to new issues at an early stage, predict problems that may arise in the future, and take measures early on.
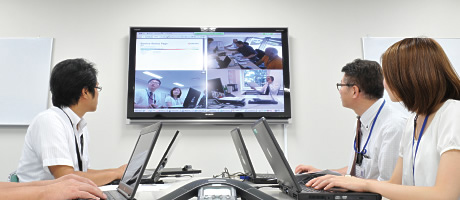
Innovations in Information Analysis
Problems that occur after a product is released to the market can serve as great references for developing and improving the product. We collect market data relating to the quality of our products and services from all over the world, analyze it, and provide feedback to the relevant departments. In order to effectively use these precious information resources, we are working to innovate data collection and analysis methods. Moving forward with the aim of making more specific and speedy proposals to resolve problems in product development, maintenance and service, we gather a wide range of data from both inside and outside Japan. This includes operational data gathered on products operating in the market, maintenance and service activity data from service personnel, maintenance parts shipment information, and call center logs. Through statistical analysis and text mining of this data, we are building a system for integrated analysis of quality risks and factors for failure. We use the analyzed data obtained from this system to continuously improve the quality of our products and services. We also identify the latent needs of customers and provide feedback for the development of new products.
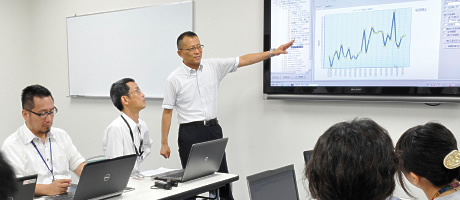
Home > Sustainability > Society > Approaches to Raising Quality and Customer Satisfaction Levels