Home > Sustainability > Society > Labor Safety Promotion System
Labor Safety Promotion System
Occupational Safety Promotion System
The Kyocera Group is committed to creating a safe and secure work environment for our employees through the Kyocera Group Environmental Safety Policy, based on our Management Rationale.
The number of occupational accidents peaked in FY2011 and has been on a downward trend since then, but is expected to increase after FY2021.
Work-related accidents generally result from deficiencies in awareness of safety procedures (training) among inexperienced employees and insufficient risk awareness for specific tasks.
In response, a system for implementing risk assessments has been created; efforts have been made to improve risk identification and countermeasures further; a revamping of the training system for inexperienced employees is under consideration; and, a new type of hazard awareness training has been introduced.
In the medium to long term, we aim to foster operational excellence through safety-focused workplaces. Employees can educate each other through safety management activities in which all employees participate.
Safety Management System of KYOCERA Document Solutions
Status of ISO 45001 certification acquisition
Integrated Certification | |
---|---|
KYOCERA Document Solutions Inc. Global Headquarters | KYOCERA Document Solutions Inc. Tamaki Plant |
KYOCERA Document Solutions Inc. Hirakata Plant | KYOCERA Document Solutions Japan Inc. (Osaka headquarters) |
Individual Certification | |
KYOCERA Document Solutions Australia |
Goals
At Kyocera Document Solutions, we are engaged in initiatives based on the "Kyocera Group Environmental Safety Targets."
●Lost time accident rate among Kyocera Document Solutions Group
Achievements in FY2024 | Lost time accident rate in Japan: 0.35 Lost time accident rate at the production sites outside of Japan: 0.02 Number of fire incidents: 0 |
Trends in the Accident Rate of the Kyocera Document Solutions Group (in Japan)
In FY 2024, the lost time accident rate for the Kyocera Document Solutions Group (in Japan) was 0.35, which is below the average for all manufacturing industries and the electrical machinery manufacturing industry. Additionally, there were zero fire incidents (with a target of zero incidents). Furthermore, for accidents that occurred in various countries, we conduct cause investigations and implement safety measures, such as eliminating hazards.
We will continue to promote initiatives aimed at reducing occupational accidents and strive to create a safe and secure working environment.
* The lost time accident rates of all manufacturing industries and electrical machinery and appliance manufacturing industries are based on data from the Ministry of Health, Labour and Welfare.
* Lost time accident rate: Number of afflicted persons / 1 million hours (The number of days of missed work is as per the standards of the Ministry of Health, Labour and Welfare.)
* The Ministry of Health, Labour and Welfare figures utilize fiscal year data. (Lost time of one day or more)
* Kyocera Document Solutions Inc. and Kyocera Document Solutions Group (in Japan) lost time accident rates utilize fiscal year data. (Lost time of one day or more)
* Temporary and part-time employees are excluded
Examples of Major Initiatives
Implementation of Risk assessment
In order to prevent accidents, in Japan, we appoint risk assessment trainers and risk assessors at each business site and continue to develop risk assessment measures. Risk assessment trainers and risk assessors receive practical training and lectures regarding the necessary base knowledge and skills. They then perform risk assessments to gain an understanding of hazards through the appropriate identification and evaluation of risks before implementing countermeasures.
This serves to prevent accidents before they occur. In addition to the previous year's efforts, special patrols were conducted within the group to identify major risks and evaluate the effectiveness of control measures, and to thoroughly address and improve activities to address major risks. We will continue to make improvements by establishing more effective risk identification methods and improving the capabilities of our risk assessment trainers and risk assessors to prevent accidents.
●Risk Assessment Overview
Hazard Awareness Training Using Virtual Reality (VR)
We run hazard awareness training that utilizes VR. Inexperienced employees are given a virtual experience of the dangers inherent in their work. This boosts their hazard awareness and makes them more safety-conscious in their actions. Through this training, we continue improving content and endeavoring to prevent industrial injury and fatalities.
Implementation of emergency measures and training
We have established response regulations for large-scale earthquakes and fire incidents, and we conduct regular comprehensive fire prevention and disaster evacuation drills, which include ensuring the safety of visitors and employees. In addition, we also regularly conduct fire extinguisher training, evacuation drills using emergency stair evacuation chairs, and first aid training.
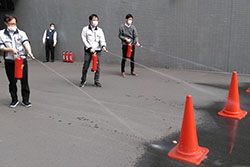
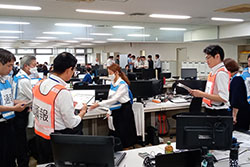
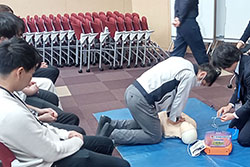
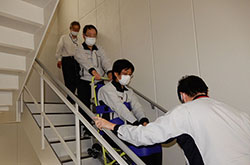
Home > Sustainability > Society > Labor Safety Promotion System